Final product check
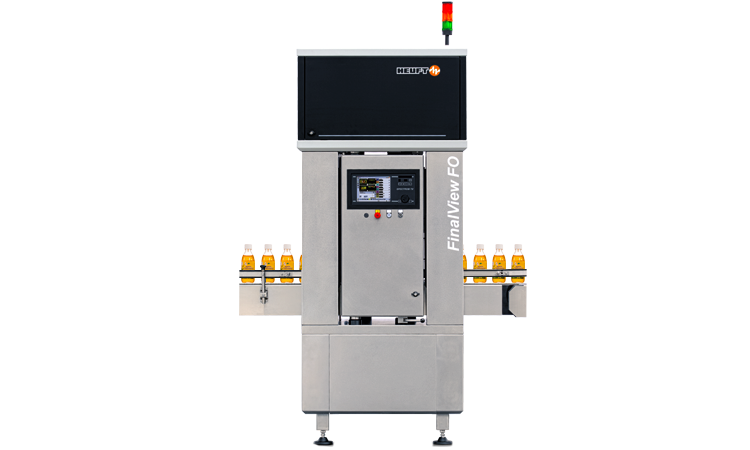
HEUFT FinalView FO6
Inspecting the container dress with high precision: a continuous final inspection.
The HEUFT FinalView FO6 carries out a detailed 360° inspection of the dress of all the formats of unaligned filled pharmaceutical containers. It achieves just as high a detection reliability when detecting incorrectly positioned, non-brand and damaged labels as when identifying minute printing and design faults. In addition the end of line system takes over, among other things, the inspection of the closures. The teach-in function of the integrated real-time image processing system learns individual quality requirements and therefore reduces the false rejection rate sustainably.
Label inspection
A complete examination: 360° inspection without blind spots.
Correct brand, readable and perfect: consumers demand the highest standards regarding the product and its packaging especially in the pharmaceutical sector. The labels have to match the contents, be correctly positioned and without folds, defects, scratches or dirt so that they are not disappointed or their health put at risk. Just as important: a perfect print image and design. The HEUFT FinalView FO6 checks these quality criteria using the most modern high-performance cameras on several levels.
Read more...
Therefore the 360° inspection of the complete container volume is always possible without any blind spots. A precisely controllable, harmonious illumination makes sure that neither reflections nor shadows can impair the detection reliability. The system also reliably differentiates between labels which only deviate due to a single minute characteristic. It even checks imprints on a background with a similar colour highly precisely. The HEUFT reflexx² technology makes specific teaching in possible: uncritical characteristics, such as a slight print offset, can be taught in as good objects with it so that they no longer cause a rejection.
Checking characteristics
Verifying product markings: reading BBDs and barcodes.
Present, readable and correct contents: the HEUFT FinalView FO6 verifies that this is true in the case of best-before dates (BBDs) and barcodes with the HEUFT vio OCR. Special illumination technology achieves optimal detection reliability even when the ambient conditions are difficult. Automatic date adaptation always keeps the code reader up to date. This eliminates the danger of products which are not marked or incorrectly marked reaching the market.
Closure detection
Ensuring tightness and brand affiliation: presence check and logo inspection.
Present, correct brand and safe: the HEUFT FinalView FO6 examines the closures using a special colour camera technology. It identifies unsealed pharmaceutical containers just as reliably as those which are not the correct brand.
Read more...
The correct colour of the lid as well as the presence, alignment, integrity and the content-related reference of the lid logo to the filled product are checked precisely. The system removes unsealed containers just as reliably as those with non-brand closures. Additional technologies can be optionally integrated in the HEUFT FinalView FO6 for an extensive closure inspection due to its modular construction.
Automatic sampling
Checking production quality regularly: exemplary sampling.
Controlled, individual and representative: the HEUFT FinalView FO6 carries out exemplary sampling for internal quality assurance purposes. Cross-sectional sampling of production is possible due to the freely definable rejection of the desired number or a whole series of containers in succession.
Read more...
In addition it is also possible to define particular conditions such as minimum speed in order to take representative samples under standard production conditions.
Fault rejection
Preventing recalls: the reliable rejection of faulty containers.
Fast, careful and accurate: highest precision when detecting faults is only effective if the products in question are also removed afterwards. The single-segment and multi-segment rejection systems of the HEUFT rejector series deal with this both precisely and carefully.
Product monitoring and self-tests
Playing it safe: exact product tracking and regular self-tests.
Always knowing the current location of a particular product: each one is tracked precisely for this. This ensures that none remain uninspected.
Read more...
The integrated reject verification checks that each product identified as faulty is really removed. Standard test programs guarantee a regular examination of the detection performance. Network-based continuous documenting and long-term archiving of the results.
Easy brand change
Changing automatically: servo-controlled adjustment of the transport and detection units.
Fast, automatic and simple: the passage width of the conveyor in the HEUFT FinalView FO6 as well as the height and position of the individual detection units adapt to the changed container format by themselves without manual intervention during program changes due to clearly reproducible brand adjustments and an innovative servo technology. This economizes on human resources and not only saves time but money as well: efficiency and productivity losses due to lengthy changeover times are sustainably decreased.
Optional additional functions
Detecting even more: extensions to the range of functions.
The HEUFT SPECTRUM systems with their modular design can be extended at any time. Thus the range of functions of the HEUFT FinalView FO6 can be optionally extended by means of the HEUFT VISION 360 to a highly precise, optical all-around closure inspection which even uncovers minute defects. Furthermore the following can be integrated upon request: powerful detection units for a precise fill level detection and internal pressure measurement.
HEUFT SPECTRUM TX
Controlling centrally: one platform for all requirements.
Precise, network-compatible and cross-system: the HEUFT SPECTRUM TX forms the basis for different technologies, modules and functions. The devices of the generation of the same name can be exactly adapted to individual requirements on site and retrofitted at any time due to this universal platform.
Read more...
A cross-system component equality of 70 per cent ensures a high availability of spare parts. The central HEUFT SPECTRUM TX control unit creates a high level of precision during continuous product tracking and quality assurance due to its multiprocessing capability. A future-proof network connection ensures reliable remote maintenance and production data acquisition for optimum efficiency and productivity. In-house developed hardware and software and its own operating system ensure computing power and offer no opportunity for viruses or malware.
HEUFT reflexx A.I.
Simply detecting more: real-time image processing with artificial intelligence.
The AI discipline of machine learning for targeted object classification has been mastered by our self-developed image processing since 2010! And since then it has learned a lot: intelligent filters distinguish drops of water on the container from air bubbles in the glass and even make it possible to identify tiny defects which are hidden behind ACLs or embossings. HEUFT reflexx A.I. now also uses deep learning!
Read more...
Appropriately trained neural networks are used for example to denoise X-ray images or to find dangerous foreign objects in structured products and to reliably distinguish them from good objects which are extremely similar in their shape, size and density. With true artificial intelligence, the hardware and software from our own development and production again increases detection reliability - and minimises the false rejection rate. The smart image processing can be directly integrated into the HEUFT reflexx A.I. camera which was developed in-house and which processes and evaluates its own images directly in real time and raises the adaptive image analysis to a top level.
HEUFT PILOT
Operating HEUFT systems reliably: graphical user interface with practical tools.
Clear, helpful and specific: the HEUFT PILOT graphical user interface convinces due to an easy to understand, multilingual menu structure with extensive auxiliary tools. Therefore the reliable operation of the HEUFT SPECTRUM TX systems is not difficult.
Read more...
Important information and clear error messages with service notes provide the respective user with specific support. This avoids incorrect adjustments and shortens standstills e.g. during brand changes. Password protected operator levels adapted to the respective area of responsibility also contribute to this. Also integrated: a complete online user manual and a tool for the uncomplicated identification and direct ordering of spare parts.
Fullscreen
Network technologies
Networking everything: online connection for increased efficiency and quality.
Information transmission in real time, production data acquisition, line analysis and remote maintenance: networking is the answer!
Read more...
HEUFT systems have future-proof network interfaces (Gigabit Ethernet and TCP / IP) for an online connection via the Internet and the database interface (SQL / DDE) for top line efficiency and an optimum quality management with considerably faster and easier workflows. Therefore production data, shift records, productivity faults and HACCP limit value analyses are available network-wide. The result: early identification of quality and efficiency problems. The firewall protected direct connection to the HEUFT TeleService makes competent remote maintenance possible all around the clock.
HEUFT rejector
Removing faulty products: the right rejector for all cases.
For example, the single-segment HEUFT flip and HEUFT mono rejectors as well as the multi-segment HEUFT DELTA-K and HEUFT DELTA-FW systems are ideally suited for the HEUFT FinalView FO6.- an end of line system in order to ensure that the product has a perfect appearance at the point of sale and that the likelihood of confusion is reduced
- homogeneous illumination and highly precise camera technology for maximum detection reliability during a continuous 360° inspection
- complete inspection of the front and back labels of unaligned containers
- detailed label and closure inspection for highest product quality and brand purity
- implementation of individual quality requirements with minimum false rejection rate due to real-time image processing system with teaching in capability
- fast and easy automatic brand changes
- numerous optional additional functions for an extensive full product inspection
- minimisation of the false rejection rate up to < 0.1%