Blow fill seal ampoule inspection
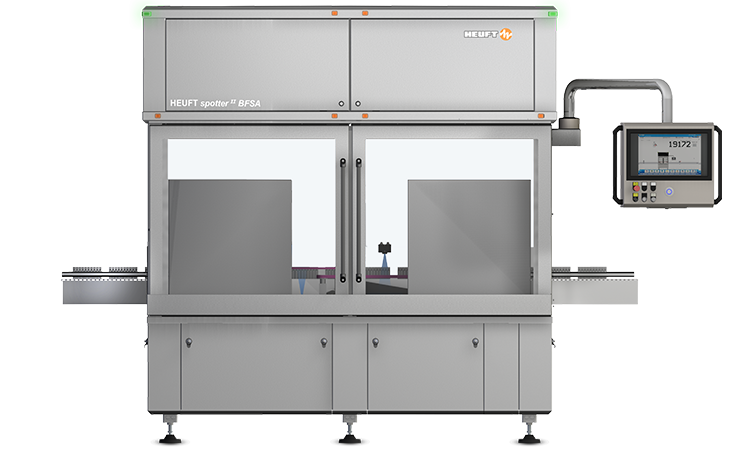
HEUFT spotter II BFSA
A one hundred percent all-around inspection of pharmaceutical blow fill seal ampoule strips based on the HEUFT SPECTRUM II.
The straight-line HEUFT spotter II BFSA has been specially developed for the all-round inspection and integrity testing of primary packaging materials for small volume parenteral products and other liquid preparations which are produced using the blow fill seal method and achieves complete reliability when detecting and rejecting faulty plastic ampoules. They identify deformations, missing or excess packaging components, soiling, scratches, scores, inclusions and cosmetic defects in the container material just as reliably as foreign particles, fill quantity and product colour deviations inside them.
Cap inspection
Ensure closure integrity: Top-down and all-around inspection.
Cosmetic defects, missing or misaligned components: The HEUFT spotter II BFSA detects closure faults such as these during the top-down inspection of filled blow fill seal ampoules. Inclusions such as black spots but also material shortages and excesses, scratches, damage and deformations on the closure as well as misaligned closures are reliably identified during the inspection of bundled ampoule strips using smart LED illumination and specially adapted camera, image filtering and subtraction technologies.
Fullscreen
Sidewall inspection
Covering everything: Alternating complete inspection.
Damage, cosmetic defects, foreign particles and fill level deviations: A full coverage inspection of the sidewalls of blow fill seal containers is essential in order to find such faults everywhere. The HEUFT spotter II BFSA realises this with sophisticated optomechanics and a specially designed transport device:
Read more...
the servo-controlled belt drive which clamps the ampoule strips and guides them straight through the device has an alternating design. In the infeed, they are "gripped" at the top to examine their entire lower part down to the bottom edge, and in the outfeed, they are then gripped at the bottom so that the entire upper half is covered there. This not only creates redundancy and thus even more detection reliability during closure inspection, but also realises complete coverage of the full volume of each individual primary packaging for small volume parenterals. From missing or excess closure components to inclusions, contaminants or inconspicuous fat deposits to fill level and product colour deviations, floating foreign particles and base deformations, all critical defects are detected regardless of their location and position.
Fullscreen
Base inspection
Getting to the bottom: Seamless inspection of the underside.
Foreign particles, inclusions, contamination and damage: To find such defects in every case, the full-cover sidewall inspection down to the bottom edge is not always sufficient. Additional safety is provided by another high-performance camera that scans the container base. This reliably identifies foreign particles that have sunk to the bottom of the container, but also black spots trapped in the base, contamination and deformations of this area. Together with the full-coverage sidewall inspection, this ensures that the entire base - including its underside - is inspected without any blind spots.
Fullscreen
Fault rejection
Preventing recalls: the reliable rejection of faulty containers.
Fast, careful and accurate: highest precision when detecting faults is only effective if the products in question are also removed afterwards. The single-segment and multi-segment rejection systems of the HEUFT rejector series deal with this both precisely and carefully.
Simple type changes
Automatic changeover: Servo-controlled adjustment of the detection and transport units.
Automatic, fast, simple: as is usual with systems based on the HEUFT SPECTRUM II platform trigger photoelectric sensors, cameras, lighting units and transport devices adjust themselves fully automatically to different sizes and types of blow-fill-seal containers. Programme and format changes can thus be carried out without tools and without any human intervention. This not only saves time, but also money: efficiency and productivity losses due to lengthy changeover times are sustainably reduced.
Product monitoring and self-tests
Playing it safe: exact product tracking and regular self-tests.
Always knowing the current location of a particular product: each one is tracked precisely for this. This ensures that none remain uninspected.
Read more...
The integrated reject verification checks that each product identified as faulty is really removed. Standard test programs guarantee a regular examination of the detection performance. Network-based continuous documenting and long-term archiving of the results.
HEUFT SPECTRUM II
Simply automating: universal device platform for maximum performance.
Highly automated, universal and powerful: the HEUFT SPECTRUM II ensures optimum detection and operational reliability during an in-line quality assurance for the sustainable safeguarding of product quality and line efficiency.
Read more...
The cross-system control unit with multiprocessing capability for different modules, systems and applications convinces due to its exceptional degree of automation. Brand and format changes can be carried out without manual intervention. The unique human machine interface of the universal device platform is self-explanatory. Human resources are effectively saved in this way. In-house developed hardware and software of the latest generation and a future-proof network connection achieve highest computing power and data transmission in real time. The result: maximum precision during purposeful product tracking, inspection and rejection.
HEUFT reflexx A.I.
Simply detecting more: real-time image processing with artificial intelligence.
The AI discipline of machine learning for targeted object classification has been mastered by our self-developed image processing since 2010! And since then it has learned a lot: intelligent filters distinguish drops of water on the container from air bubbles in the glass and even make it possible to identify tiny defects which are hidden behind ACLs or embossings. HEUFT reflexx A.I. now also uses deep learning!
Read more...
Appropriately trained neural networks are used for example to denoise X-ray images or to find dangerous foreign objects in structured products and to reliably distinguish them from good objects which are extremely similar in their shape, size and density. With true artificial intelligence, the hardware and software from our own development and production again increases detection reliability - and minimises the false rejection rate. The smart image processing can be directly integrated into the HEUFT reflexx A.I. camera which was developed in-house and which processes and evaluates its own images directly in real time and raises the adaptive image analysis to a top level.
HEUFT NaVi
Simply knowing what to do: self-explanatory audiovisual user guidance.
Intuitive, individual and audiovisual: previous knowledge is not required in order to operate the HEUFT SPECTRUM II systems reliably. The HEUFT NaVi user guidance is self-explanatory and supports the respective user step by step.
Read more...
An RFID login with user-related access rights provides an overview and makes the respective user's work simply easy: he only sees what he really needs to on the clearly arranged touchscreen user interface with a flat menu structure, integrated tutorials and precise auxiliary tools in order to fulfil his specific tasks optimally. He is supported by a virtual assistant in the course of this. She speaks to him and clearly explains what has to be done when and where. Purposeful and focussed on the essentials – the audiovisual HEUFT NaVi user guidance makes the reliable operation of HEUFT systems simply easy!
HEUFT checkPoints
Simply seeing where what has to be done: trouble-free localisation.
Clear, direct and purposeful: the user can cope immediately on the rare occasions when manual intervention is needed. Because eye-catching HEUFT checkPoints make it clear at a glance exactly when it is necessary to take matters in hand in addition to the audiovisual information which the HEUFT NaVi provides.
Read more...
The orange tags not only flash on the touchscreen but also at the respective component if the worst comes to the worst. The problem is located without a long search. This saves time and human resources, shortens standstills and therefore increases productivity.
Network technologies
Simply capture everything: Network connectivity for performance analysis and audit trail documentation.
Computer-aided systems for the packing and quality assurance of pharmaceuticals must fulfil strict requirements and documentation obligations. This is another reason why HEUFT devices are network-capable. With user-related access rights and a detailed audit trail log of all operating and process information they fulfil the FDA's 21 CFR Part 11 requirements. This protects against unwanted parameter changes and makes all logins permanently traceable. An online connection to higher-level databases and MES systems ensures real-time transmission, processing and complete archiving of detection images, batch and production data as well as reliable audit trail documentation. There is a network connection to the HEUFT TeleService for reliable remote diagnosis and maintenance.
Linear construction
Run in a linear way: Compact straight-forward system.
In addition to its functionality and automation the HEUFT spotter II BFSA is distinguished above all by its consistent linear operation. This makes it extremely compact, enables fully automatic sort and product changes and reduces storage costs. In addition it is ensured that the sensitive BFS containers are handled gently with the highest possible throughput. After all, they are supposed to detect defects instead of producing them themselves. Specially designed conveyors ensure gentle handling of the space-saving straight runner.
HEUFT CleanDesign
Cleaning quite simply: hygiene-optimised construction.
Accessible, clean and safe: its HEUFT CleanDesign predestines the system for use in hygienically sensitive areas.
Read more...
Sloping surfaces facilitate cleaning and prevent the accumulation of stubborn dirt. Special channels and openings allow the liquids required for cleaning purposes to be drained off completely. Consequently dangerous germs and bacteria have no contact surface whatsoever. Specially constructed casings and doors create optimum accessibility. The electronics are totally encapsulated. Sensitive areas such as the inspection units are dust-proof and protected against contact as well as water jets.
HEUFT rejector
Sorting out faulty BFS containers: Accurate rejection.
Targeted, safe, reliable: Different single or multi-segment rejection systems can be connected to the HEUFT spotter II BFSA in order to remove individual or bundled blow-fill-seal ampoule strips which have been detected as faulty from circulation in good time. They consistently remove pharmaceutical blow-fill-seal containers with safety and quality defects from the production flow so that only faultless ones reach the patient.
- complete all-around inspection for defect-free BFS primary packaging for the safe administration of vaccines and other small-volume parenterals
- precise identification of damage, deformations, foreign particles, faulty fillings, product colour deviations and cosmetic defects
- 100% high-speed integrity testing of blow-fill-seal ampoule strips
- highly automated HEUFT SPECTRUM II system in an efficient, space-saving straight line configuration
- minimal maintenance costs, easy programme changes and long-term operational reliability due to the fact that there are no format parts which are susceptible to wear and tear
- highly reliable technological environment thanks to adaptive special lighting, state-of-the-art optomechanics and image processing, image filtering and image subtraction technologies developed in-house and tailored to specific inspection tasks
- future-proof network connection, e.g. for complete audit trail documentation and online remote maintenance
- reliable compliance with basic FDA, GMP, GAMP5 and 21 CFR Part 11 requirements