Closure inspection
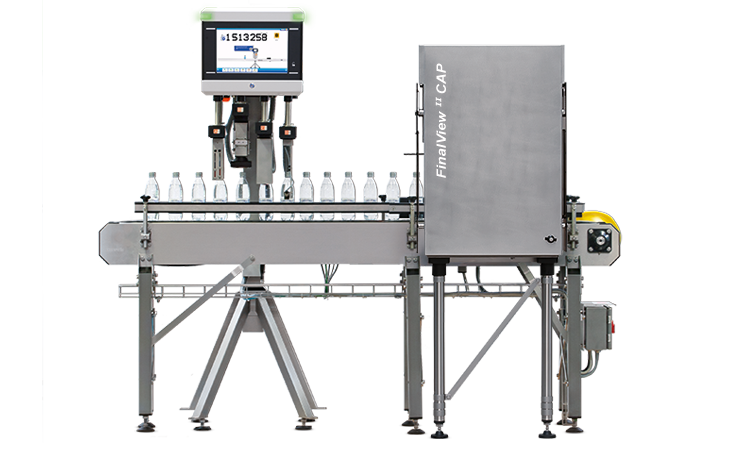
HEUFT FinalView II CAP
Detailed 360° closure inspection based on the HEUFT SPECTRUM II.
All-around, continuous, highly precise and simply easy: the HEUFT FinalView II CAP takes the in-line inspection of bottle closures to a new level. Thus the compact add-on module which is straightforward to connect to HEUFT SPECTRUM II full container inspectors safeguards the integrity and quality of the filled end product sustainably.
Presence check and colour logo inspection
Protecting quality and brand: reliable identification of unsealed or non-brand containers.
Present, correct brand and safe: the HEUFT FinalView II CAP carries out a complete all-around inspection of the closures using innovative optical technologies. It goes far beyond merely checking the presence: not only unsealed beverage containers are reliably identified but also those with non-brand closures. Powerful colour cameras and a real-time image processing system capable of learning make deviating colouration, designs, lettering and lid logos clearly visible for this purpose. In this way the quality and the microbial purity of the bottle contents are protected as well as the dress of the finished branded product regarding correct brand and distinctiveness.
Fullscreen
Closure position and roll on inspection
Showing the contour: reliable detection of canted closures and thread faults.
Straight, firm and tight: the closures of beverage containers must fit correctly. Crooked, canted screw closures, flagging tamper evident rings or thread faults not only threaten the functionality of the closures but also their tightness and with that the integrity of the product. The HEUFT FinalView II CAP measures the contour of each individual closure area exactly from different perspectives and compares the results with the correct reference values. Canted closures, incorrectly positioned safety elements, bullnoses, protruding wine corks and many other deviations are therefore reliably revealed. The roll on and profile inspection even goes one step further and checks the presence and shape of the thread turns of each individual screw closure precisely. Therefore bottles which cannot be opened safely or are not tightly sealed are exposed in good time.
Fullscreen
All-around closure inspection in colour
Clearly identifying tiny safety defects: continuous inspection of the closure walls.
Attractive, intact and safe: closure walls and safety elements have to be free from defects. That is the only way that they can perform their tasks and prevent product leakage and contamination effectively. Whether cracks, damage or chips in the closure wall, faulty tamper evident and carrying rings, scratched capsules or improperly flanged sparkling wine bottle agrafes: the compact detection unit identifies all kinds of defects using innovative illumination, camera and real-time image processing technologies. The high-resolution all-around colour inspection covers far more than 360° in the course of this – blind areas are therefore finally things of the past.
Angle of rotation detection with millimetre accuracy
Aligning correctly: precise inspection of the closure position.
Correctly applied, reliably sealed and exactly oriented: not infrequently it all depends on the relative fit of the bottle closure too. Is it at the right angle to corresponding marking on the carrying ring or on the bottle neck? In other words: is it really aligned as it is supposed to be? The HEUFT FinalView II CAP checks this using a special angle of rotation detection. It compares the results of the colour logo and closure wall inspections with each other. In this way the correct orientation of the closure can be checked with millimetre accuracy. Thus neither logos nor lettering are distorted any more. All the closures are indeed exactly aligned as they are supposed to be.
Fault rejection
Preventing recalls: the reliable rejection of faulty containers.
Fast, careful and accurate: highest precision when detecting faults is only effective if the products in question are also removed afterwards. The single-segment and multi-segment rejection systems of the HEUFT rejector series deal with this both precisely and carefully.
Fullscreen
Product monitoring and self-tests
Playing it safe: exact product tracking and regular self-tests.
Always knowing the current location of a particular product: each one is tracked precisely for this. This ensures that none remain uninspected.
Read more...
The integrated reject verification checks that each product identified as faulty is really removed. Standard test programs guarantee a regular examination of the detection performance. Network-based continuous documenting and long-term archiving of the results.
HEUFT SPECTRUM II
Simply automating: universal device platform for maximum performance.
Highly automated, universal and powerful: the HEUFT SPECTRUM II ensures optimum detection and operational reliability during an in-line quality assurance for the sustainable safeguarding of product quality and line efficiency.
Read more...
The cross-system control unit with multiprocessing capability for different modules, systems and applications convinces due to its exceptional degree of automation. Brand and format changes can be carried out without manual intervention. The unique human machine interface of the universal device platform is self-explanatory. Human resources are effectively saved in this way. In-house developed hardware and software of the latest generation and a future-proof network connection achieve highest computing power and data transmission in real time. The result: maximum precision during purposeful product tracking, inspection and rejection.
Fullscreen
HEUFT reflexx A.I.
Simply detecting more: real-time image processing with artificial intelligence.
The AI discipline of machine learning for targeted object classification has been mastered by our self-developed image processing since 2010! And since then it has learned a lot: intelligent filters distinguish drops of water on the container from air bubbles in the glass and even make it possible to identify tiny defects which are hidden behind ACLs or embossings. HEUFT reflexx A.I. now also uses deep learning!
Read more...
Appropriately trained neural networks are used for example to denoise X-ray images or to find dangerous foreign objects in structured products and to reliably distinguish them from good objects which are extremely similar in their shape, size and density. With true artificial intelligence, the hardware and software from our own development and production again increases detection reliability - and minimises the false rejection rate. The smart image processing can be directly integrated into the HEUFT reflexx A.I. camera which was developed in-house and which processes and evaluates its own images directly in real time and raises the adaptive image analysis to a top level.
Fullscreen
HEUFT NaVi
Simply knowing what to do: self-explanatory audiovisual user guidance.
Intuitive, individual and audiovisual: previous knowledge is not required in order to operate the HEUFT SPECTRUM II systems reliably. The HEUFT NaVi user guidance is self-explanatory and supports the respective user step by step.
Read more...
An RFID login with user-related access rights provides an overview and makes the respective user's work simply easy: he only sees what he really needs to on the clearly arranged touchscreen user interface with a flat menu structure, integrated tutorials and precise auxiliary tools in order to fulfil his specific tasks optimally. He is supported by a virtual assistant in the course of this. She speaks to him and clearly explains what has to be done when and where. Purposeful and focussed on the essentials – the audiovisual HEUFT NaVi user guidance makes the reliable operation of HEUFT systems simply easy!
Fullscreen
HEUFT checkPoints
Simply seeing where what has to be done: trouble-free localisation.
Clear, direct and purposeful: the user can cope immediately on the rare occasions when manual intervention is needed. Because eye-catching HEUFT checkPoints make it clear at a glance exactly when it is necessary to take matters in hand in addition to the audiovisual information which the HEUFT NaVi provides.
Read more...
The orange tags not only flash on the touchscreen but also at the respective component if the worst comes to the worst. The problem is located without a long search. This saves time and human resources, shortens standstills and therefore increases productivity.
Network technologies
Networking everything: online connection for increased efficiency and quality.
Information transmission in real time, production data acquisition, line analysis and remote maintenance: networking is the answer!
Read more...
HEUFT systems have future-proof network interfaces (Gigabit Ethernet and TCP / IP) for an online connection via the Internet and the database interface (SQL / DDE) for top line efficiency and an optimum quality management with considerably faster and easier workflows. Therefore production data, shift records, productivity faults and HACCP limit value analyses are available network-wide. The result: early identification of quality and efficiency problems. The firewall protected direct connection to the HEUFT TeleService makes competent remote maintenance possible all around the clock.
HEUFT CleanDesign
Cleaning quite simply: hygiene-optimised construction.
Accessible, clean and safe: its HEUFT CleanDesign predestines the system for use in hygienically sensitive areas.
Read more...
Sloping surfaces facilitate cleaning and prevent the accumulation of stubborn dirt. Special channels and openings allow the liquids required for cleaning purposes to be drained off completely. Consequently dangerous germs and bacteria have no contact surface whatsoever. Specially constructed casings and doors create optimum accessibility. The electronics are totally encapsulated. Sensitive areas such as the inspection units are dust-proof and protected against contact as well as water jets.
Fullscreen
HEUFT rejector
Removing faulty products: the right rejector for all cases.
For example, the single segment HEUFT flip and HEUFT mono rejectors as well as the multi-segment HEUFT DELTA-K and HEUFT DELTA-FW systems are ideally suited for the HEUFT FinalView II CAP.- effective brand and product protection due to maximum closure safety
- extremely space-saving, easy to integrate add-on module for fill management systems and full container inspectors such as the HEUFT SPECTRUM II VX and the HEUFT squeezer II QS
- a cleverly devised combination of different optical high performance technologies for utmost precision during the completely continuous all-around inspection of each individual closure at up to 100,000 containers per hour
- twice as many colour cameras and six times higher resolution than previous HEUFT solutions for inspecting closures
- increase in the maximum diameter of closures which can be completely inspected by a factor of 1.5
- increase in the possible height difference between the smallest and the largest full bottle which can be reliably inspected to 30 centimetres
- highly automated HEUFT SPECTRUM II system with brand and format changes at the touch of a button