Fill management
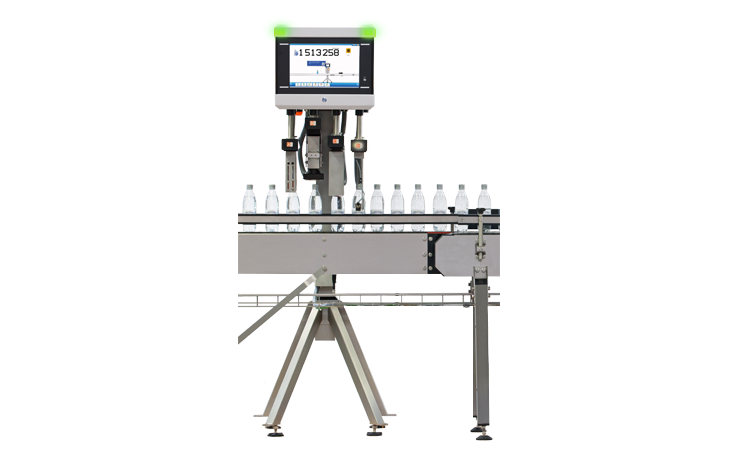
HEUFT SPECTRUM II VX
Finding fill level and closure faults just as easily as their causes: fill management based on the HEUFT SPECTRUM II.
Ensuring the highest product quality with maximum filler and closer efficiency – with the HEUFT SPECTRUM II VX this is simply easy! Proven functions for checking and inspecting full containers safeguard the quality of the products. The system uncovers losses in filler and closer performance before this can impair the efficiency of the complete line using an integrated quantifying system, serial fault detection and continuous monitoring. The high degree of automation of the HEUFT SPECTRUM II platform and the self-explanatory HEUFT NaVi user guidance take fill management to a new level.
Fill level detection
Finding underfills and overfills reliably: the right technology for each application.
Too little, too much and exactly right: the HEUFT SPECTRUM II VX can be perfectly equipped with different detection modules for a precise fill level detection.
Read more...
Special camera technology checks the filling quantity of transparent bottles highly precisely. The high frequency measurement provides exact results for all types of non-metal containers – and compensates foam which may be present in the course of this. This reduces the false rejection rate on filling lines for beer or carbonated soft drinks. X-ray technology for determining the filling quantity exactly is used if the containers are opaque. An integrated quantifying module converts the results of the individual fill level measurements automatically into the actual fill value and calculates the average fill volume.
Fullscreen
Closure detection
Ensuring tightness: different possibilities for a closure check.
Effective, safe and precise: different technologies for a closure check can be integrated into the system due to its modular construction. It can check the presence, position, completeness, integrity and brand affiliation of the closures precisely with special sensor, camera or ultrasonic technology depending on the requirements. Thus it provides the best results for every application and safeguards the tightness of the bottle sustainably as well as the quality of the product contained in it.
Fullscreen
Filler and closer management
Finding faults and exposing the causes: monitoring the filler valves and the closer heads.
Detecting, monitoring and locating: finding faulty filling and closure faults reliably is one thing. However it is just as important to uncover their causes at an early stage for the sustainable safeguarding of product quality and productivity.
Read more...
The HEUFT SPECTRUM II VX takes over the monitoring of the filler valves and closure heads for this purpose. It monitors their performance continuously and provides exact statistical data. Malfunctions which can cause serial faults are therefore identified in good time. The system exposes defective valves and closure heads even before they completely fail. This permanent filler and closer management system is a valuable tool for preventive maintenance.
Fullscreen
Burst bottle management
Detecting and competently managing burst bottles: effective protection against contamination due to glass splinters.
Detection, reaction and prevention: the potential danger of glass bottles which burst in the filler should not be underestimated. The HEUFT SPECTRUM II VX registers burst bottles immediately and draws the right conclusions: not only are these rejected but also adjacently filled bottles and those which have been filled during the subsequent circuits with the same valve. Therefore products contaminated with glass splinters cannot reach the customer.
Read more...
Furthermore an optional forced underfill can prevent them from being inadvertently returned to the production flow. Another safety factor is provided by the shower function which cleans the areas which could be contaminated with glass splinters.
Fullscreen
Automatic sampling
Checking production quality regularly: exemplary sampling.
Controlled, individual and representative: the HEUFT SPECTRUM II VX carries out exemplary sampling for internal quality assurance purposes. Cross-sectional sampling is possible due to the freely definable rejection of the desired number or a whole series of bottles in succession.
Read more...
These can be selected separately for targeted sampling in order to check individual filler valves or closer heads specifically. In addition it is also possible to define particular conditions such as minimum speed in order to take representative samples under standard production conditions.
Fullscreen
Container distribution
Dividing up the production flow: distribution onto several lanes.
Specific, smooth and effective: the HEUFT SPECTRUM II VX distributes the container flow onto up to seven transport lanes if required. The distribution ratio is freely selectable and adjustable. Special jam switches ensure an even utilisation of the lanes – full conveyor sections are identified and excluded from the laning process. The result: considerably better efficiency for the whole line.
Fullscreen
Fault rejection
Preventing recalls: the reliable rejection of faulty containers.
Fast, careful and accurate: highest precision when detecting faults is only effective if the products in question are also removed afterwards. The single-segment and multi-segment rejection systems of the HEUFT rejector series deal with this both precisely and carefully.
Fullscreen
Product monitoring and self-tests
Playing it safe: exact product tracking and regular self-tests.
Always knowing the current location of a particular product: each one is tracked precisely for this. This ensures that none remain uninspected.
Read more...
The integrated reject verification checks that each product identified as faulty is really removed. Standard test programs guarantee a regular examination of the detection performance. Network-based continuous documenting and long-term archiving of the results.
Optional additional functions
Detecting even more: extensions to the range of functions.
The HEUFT SPECTRUM II systems with their modular design can be extended at any time. Therefore the range of functions of the HEUFT SPECTRUM II VX can be extended with technologies for checking the presence and position of labels. Furthermore the following can be integrated without any problems: the HEUFT vio OCR for an optical inspection of best-before dates and barcodes.
Read more...
In addition the HEUFT VISION 360 module carries out a high-precision optical closure inspection as an option. The HEUFT sonic checks the tightness of metal closures. This can also be optimally achieved when extending it with the HEUFT magnetic tracking when the closures of different manufacturers are used. The HEUFT O2 add-on detects residual air in the bottle which causes the product to spoil prematurely e.g. in the case of unpasteurized beers.
The acoustic burst bottle detection, available upon request, can even uncover partially burst bottles reliably.
Fullscreen
HEUFT SPECTRUM II
Simply automating: universal device platform for maximum performance.
Highly automated, universal and powerful: the HEUFT SPECTRUM II ensures optimum detection and operational reliability during an in-line quality assurance for the sustainable safeguarding of product quality and line efficiency.
Read more...
The cross-system control unit with multiprocessing capability for different modules, systems and applications convinces due to its exceptional degree of automation. Brand and format changes can be carried out without manual intervention. The unique human machine interface of the universal device platform is self-explanatory. Human resources are effectively saved in this way. In-house developed hardware and software of the latest generation and a future-proof network connection achieve highest computing power and data transmission in real time. The result: maximum precision during purposeful product tracking, inspection and rejection.
Fullscreen
HEUFT reflexx A.I.
Simply detecting more: real-time image processing with artificial intelligence.
The AI discipline of machine learning for targeted object classification has been mastered by our self-developed image processing since 2010! And since then it has learned a lot: intelligent filters distinguish drops of water on the container from air bubbles in the glass and even make it possible to identify tiny defects which are hidden behind ACLs or embossings. HEUFT reflexx A.I. now also uses deep learning!
Read more...
Appropriately trained neural networks are used for example to denoise X-ray images or to find dangerous foreign objects in structured products and to reliably distinguish them from good objects which are extremely similar in their shape, size and density. With true artificial intelligence, the hardware and software from our own development and production again increases detection reliability - and minimises the false rejection rate. The smart image processing can be directly integrated into the HEUFT reflexx A.I. camera which was developed in-house and which processes and evaluates its own images directly in real time and raises the adaptive image analysis to a top level.
Fullscreen
HEUFT NaVi
Simply knowing what to do: self-explanatory audiovisual user guidance.
Intuitive, individual and audiovisual: previous knowledge is not required in order to operate the HEUFT SPECTRUM II systems reliably. The HEUFT NaVi user guidance is self-explanatory and supports the respective user step by step.
Read more...
An RFID login with user-related access rights provides an overview and makes the respective user's work simply easy: he only sees what he really needs to on the clearly arranged touchscreen user interface with a flat menu structure, integrated tutorials and precise auxiliary tools in order to fulfil his specific tasks optimally. He is supported by a virtual assistant in the course of this. She speaks to him and clearly explains what has to be done when and where. Purposeful and focussed on the essentials – the audiovisual HEUFT NaVi user guidance makes the reliable operation of HEUFT systems simply easy!
Fullscreen
HEUFT checkPoints
Simply seeing where what has to be done: trouble-free localisation.
Clear, direct and purposeful: the user can cope immediately on the rare occasions when manual intervention is needed. Because eye-catching HEUFT checkPoints make it clear at a glance exactly when it is necessary to take matters in hand in addition to the audiovisual information which the HEUFT NaVi provides.
Read more...
The orange tags not only flash on the touchscreen but also at the respective component if the worst comes to the worst. The problem is located without a long search. This saves time and human resources, shortens standstills and therefore increases productivity.
Network technologies
Networking everything: online connection for increased efficiency and quality.
Information transmission in real time, production data acquisition, line analysis and remote maintenance: networking is the answer!
Read more...
HEUFT systems have future-proof network interfaces (Gigabit Ethernet and TCP / IP) for an online connection via the Internet and the database interface (SQL / DDE) for top line efficiency and an optimum quality management with considerably faster and easier workflows. Therefore production data, shift records, productivity faults and HACCP limit value analyses are available network-wide. The result: early identification of quality and efficiency problems. The firewall protected direct connection to the HEUFT TeleService makes competent remote maintenance possible all around the clock.
HEUFT rejector
Removing faulty products: the right rejector for all cases.
For example, the single segment HEUFT flip and HEUFT mono rejectors as well as the HEUFT DELTA-K and HEUFT DELTA-FW multi-segment systems are ideally suited for the HEUFT SPECTRUM II VX.
- reliable detection of all the critical faults during the filling process
- avoidance of costly production downtimes due to the early diagnosis of filler and closer malfunctions
- optimal instrument for preventive maintenance
- reliable determination and statistical processing of the average fill volume
- effective protection against contamination due to glass splinters in the case of burst bottles
- highly automated HEUFT SPECTRUM II platform with self-explanatory HEUFT NaVi user guidance
- minimum false rejection rate due to the HEUFT reflexx² real-time image processing system with teaching in procedure
- minimisation of the false rejection rate of up to 0.01%
- performance range – up to 100,000 containers per hour