Full case check
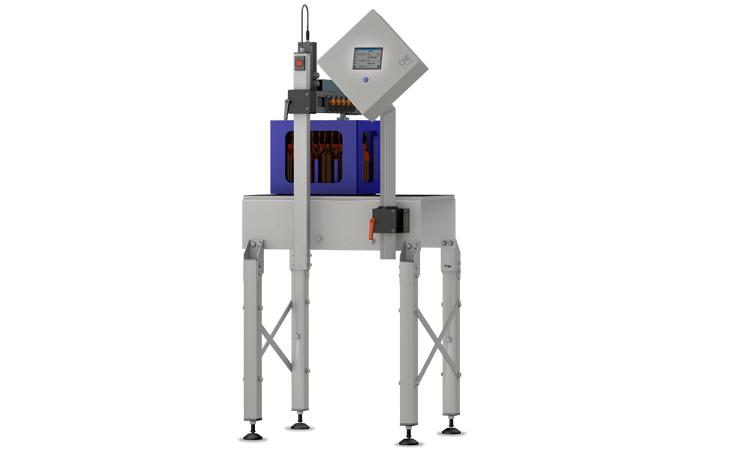
HEUFT logic II LS
Finding gaps: sorting out incomplete full cases.
At the point of sale, customers expect returnable beverage crates to be complete and sorted by brand. The same applies to other full containers. The HEUFT logic II LS checks this and removes secondary packaging containing missing containers from circulation just as reliably as it does packaging with the wrong color or labeling.
Overheight check
Avoid subsequent errors: outstanding detection.
Don't fly too high: even before the actual full container check, the HEUFT logic II LS uses an infrared photocell installed directly on the conveyor belt to detect crates, cartons, and trays with contents that are too high and protrude above their upper edge. In the worst case, such foreign bottles and objects not only threaten the overall production quality, but also the functionality of subsequent recognition modules and units in the filling and packaging porcess. To prevent this from happening, the HEUFT logic II LS triggers a belt stop in such cases. The overheight full container can thus be removed in good time.
Fullscreen
Presence and completeness check
Show presence: Gapless control.
Fully equipped: To check whether this is really the case for every full container, the HEUFT logic II LS uses a recognition bar installed on the conveyor. Depending on the container size and the number of compartments it contains, it is equipped with a different number of sensors. They check each individual compartment optically, inductively or using ultrasound and report to the compact control unit in real time if one or more of them is not sufficiently filled.
Fullscreen
Colour and barcode detection
Show your colors: checking sort affiliation.
Does the box match the contents? Camera inspection of its outer wall clarifies this and reliably detects boxes with non-brand colors. For clear product identification, it even goes one step further and checks up to 13-digit EAN and UPC barcodes on the outer wall of the respective full container. If the color or barcode and article number do not match the variety currently being processed, the full container in question is removed from the production flow.
Rejecting faulty products and sampling
Preventing recalls: reliable rejection of faulty cases.
Fast, careful and accurate: highest precision when detecting faults is only effective if the products in question are also removed afterwards. The device either emits a conveyor stop signal or activates the corresponding rejection system, such as the HEUFT maxi-laner, in order to remove incomplete cases, cardboard boxes or trays from the production flow.
Fullscreen
Product monitoring and self-tests
Playing it safe: exact product tracking and regular self-tests.
Always knowing the current location of a particular product: each one is tracked precisely for this. This ensures that none remain uninspected.
Read more...
The integrated reject verification checks that each product identified as faulty is really removed. Standard test programs guarantee a regular examination of the detection performance. Network-based continuous documenting and long-term archiving of the results.
Simple brand changes
Automatic changeover: adjustment of the recognition units.
Simply easy: with the HEUFT logic II LS, changing to other container types, colors, or formats is child's play, even for inexperienced users. This is already ensured by the self-explanatory HEUFT NaVi user guidance of the compact device. An integrated changeover assistant provides effective step-by-step assistance during the adjustment of the recognition units. Incorrect settings are thus virtually impossible, and excessive downtimes and the associated losses in productivity are no longer an issue.
Compact control unit
Processing recognition data: easy control.
The HEUFT logic II LS identifies container errors directly on the conveyor belt. Both the sensor bar for presence and completeness checks and the camera technology for color and label recognition are accommodated there in a space-saving manner. The information flows to the central control unit, where it is processed in real time and forwarded to the connected rejection system, for example. As the central communication unit, the compact control unit provides users with all the important information and a user interface with touchscreen for reliable operation of the container inspection system.
HEUFT NaVi
Simply know what to do: self-explanatory user guidance.
Intuitive, individual: no extensive prior knowledge is required to operate the HEUFT logic II LS reliably. The HEUFT NaVi user guidance is self-explanatory and supports the respective user step by step. An RFID login with user-specific access rights creates clarity and makes the respective user's work simply easy: on the tidy touchscreen user interface with a flat menu structure, they only see what they actually need to optimally perform their specific tasks. Targeted and focused on the essentials, the HEUFT NaVi user guidance makes the reliable operation of the HEUFT logic II LS simply easy!
Fullscreen
HEUFT case rejector
Removing faulty cases from circulation: the right rejector for all cases.
Discharging, rejecting and distributing: HEUFT rejection systems for packaging remove faulty crates, cardboard boxes, trays or shrink wrap packages reliably from the production flow. They achieve maximum performance optimally matched to their respective task with regard to precision and carefulness.
- fully automatic monitoring of the product quality
- presence, completeness and barcode checking
- up to 7,200 full containers per hour
- up to 16 types and production programs
- height-adjustable detection units for checking containers of different sizes
- splash-proof and dust-protected control unit with 5-inch touch screen
- self-explanatory HEUFT NaVi user guidance with changeover assistant for simple type and program changes
- space-saving design for easy integration into existing lines